If you are interested in some of our products, please feel free to visit our website or contact us for detailed information.
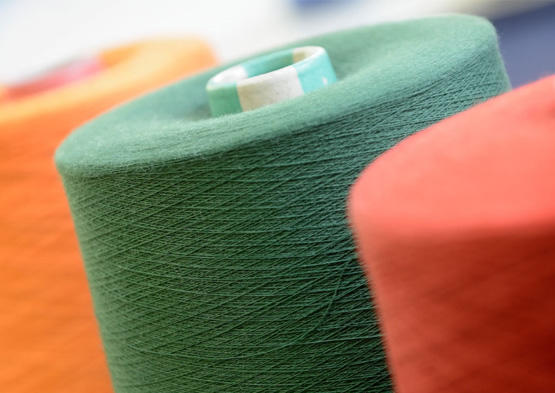
The outer fiber layer in mechanical covered yarn is the primary surface in contact with dye baths, and its chemical composition directly influences the dye class compatibility. For example, polyamide outer fibers bond well with acid dyes, while cotton requires reactive or direct dyes. Polyester, being highly crystalline and hydrophobic, only accepts disperse dyes through high-temperature or carrier-assisted dyeing. If the outer fiber does not align with the intended dye chemistry, the result can be incomplete penetration, blotchy coloration, or muted hues. When dyeing efficiency is compromised, users may be forced to compensate with deeper shade formulas, higher dye concentrations, or longer processing times, all of which increase cost and risk reproducibility issues across batches.
Many covered yarns are made with blended or customized fiber compositions. If the outer yarn includes a mixture of fibers—say, a nylon-polyester blend—the dyer must navigate dual-dye systems or sequential dyeing. This complicates color matching, especially in bulk production. A common issue arises when one fiber absorbs more dye than the other, resulting in tonal inconsistency or ‘shadowing’ under different lighting conditions. The presence of dissimilar fiber types on the surface requires precise dyeing protocol adjustments, such as controlling pH, temperature ramps, and auxiliary combinations to level the final shade.
The evenness and tightness of the mechanical covering—meaning how well the outer fibers wrap around the core—are critical for dye uniformity. Tightly wrapped yarns ensure a smooth, continuous dyeable surface, giving consistent color results. On the other hand, loosely wrapped yarns may show exposed sections of the inner core (often made from elastane, spandex, or other non-dyeable materials), which can appear as white or pale streaks after dyeing. This is especially problematic in stretch fabrics or garments where the yarn is under tension during wear or finishing, further exposing any core irregularities. Dyehouse operators often use tension-control testing and optical inspection to detect poor coverage prior to dyeing.
Yarn surface texture plays a major role in final fabric appearance after dyeing. For example, smooth, filament-based outer layers reflect more light and exhibit higher luster post-dyeing, which enhances vibrancy. Conversely, textured or matte-finish outer yarns yield flatter, more subdued tones, even when using the same dye recipe. Textured yarns absorb dye more irregularly due to their rough surface, often leading to uneven reflection, making the fabric look blotchy or grainy. These optical effects can’t be corrected post-dye and must be anticipated during yarn selection.
In a mechanically covered yarn, the core material (e.g., spandex, elastane, or polyurethane monofilament) is usually undyeable. If the outer fiber wrap is insufficient or misaligned, the dye bath does not mask the core effectively, and visible white or translucent areas may appear on the fabric post-dyeing. This issue is especially pronounced in lightweight fabrics, under tension, or when light colors are dyed. This core show-through not only affects the aesthetics but can also result in customer claims or quality downgrades. Some mills use pre-screening tests, such as magnified yarn cross-section imaging or yarn tension simulations, to ensure full coverage.
Consistency in shade across fabric panels, rolls, or garments is a major challenge when using mechanical covered yarns. If one batch has a slightly looser wrap or uses an outer fiber with a different lot of dye affinity, it could yield fabrics with seam mismatches, panel shadows, or inconsistent depth under various lighting conditions. In worst cases, garments dyed in bulk may show "body mapping" — where different zones of the same garment take on varying shades. This is unacceptable in fashion and sportswear segments.